炼油生产工艺
炼油工艺概述
炼油工艺一般是指将原油加工成各种燃料(汽油、煤油、柴油)、润滑油、石蜡、沥青等石油产品或石油化工原料(如正构烷烃、苯、甲苯、二甲苯等)的工艺过程。石油炼制一般的过程是先将原油切割成各种不同沸程的馏分,然后将这些馏分或者按照产品规格要求,除去其中的非理想组分和有害杂质,或者经过化学转化形成所需要的组分,进而加工成产品。
石油炼制的主要工艺过程大致可分为五类:
分离过程——电脱盐、常减压蒸馏
转化过程——催化裂化、加氢裂化、渣油加氢处理、延迟焦化、减粘裂化等
精制和改质过程——加氢精制、催化重整、中压加氢改质、S-Zorb等
炼厂气加工过程——烷基化、醚化、苯与乙烯烃化等
润滑油生产过程
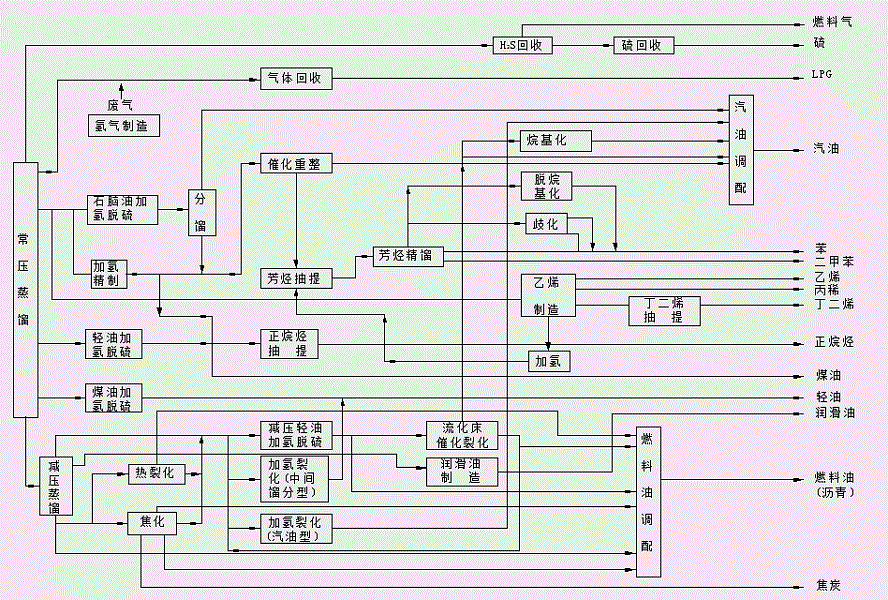
分离工艺
原油分离工艺一般包括原油脱盐脱水和原油蒸馏两个过程
原油脱盐脱水
从油藏中采出的原油都含有水和盐,原油中的盐一般为Na、Ca、Mg的氯化物或盐酸盐。原油虽然在油田经过脱盐脱水,但不能满足炼厂加工的要求,需要在炼厂进一步脱除。水和盐的存在对炼油带来的危害主要表现在:使原油蒸馏操作不稳定,对设备和管线的腐蚀;对换热器等设备造成结垢使换热效率下降,使催化剂污染或中毒。因此炼厂一般要求将原油的盐脱至<3mg/L,目前炼厂原油脱盐脱水几乎多采用二级电脱盐法
在原油中加入一定量的水和破乳剂并经混合设施充分混合后进入脱盐罐,在高压电场作用下,使小水滴聚合成大水滴,然后借助重力作用沉降分离,破乳剂的选用对脱盐效果影响很大,不同原油所用的破乳剂类型和使用量须经过试验来确定。
进入脱盐罐的原油需先加热至90~130℃,以降低原油黏度,脱盐罐要保持一定压力以防止原油汽化。
电脱盐罐一般为卧式,内设2~3层电极板,极板间距200~300mm,电场强度一般为800~900V/cm。
分离原油蒸馏
蒸馏是石油炼制必须的第一道工序。借助于蒸馏过程将原油按炼厂所要求的产品方案切割成各种馏分,然后再去加工成各种石油产品。蒸馏装置设计和操作的好坏,对整个炼厂有着十分重要的影响。
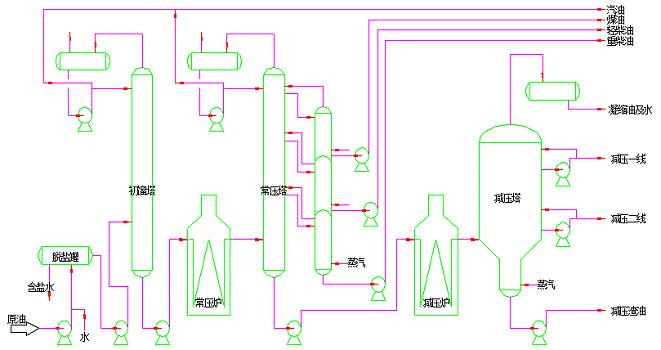
三段汽化常减压蒸馏工艺流程
原油蒸馏一般采用三级蒸馏(初馏塔或蒸发塔、常压塔、减压塔),轻馏分少的原油也可只用二级蒸馏(常压塔、减压塔)。
初馏塔一般分出原油的汽油组分,以减少换热系统和加热炉压降,常压塔一般将原油中沸点<360℃馏分切割成汽油(或石脑油)、煤油(喷气燃料或灯用煤油)、柴油馏分。各侧线抽出馏分一般都经过汽提塔以脱除轻质组分,保证产品合格。
减压塔则将沸点>360℃的常压重油切割成制取各种润滑油和石蜡的原料,或作为催化裂化、加氢裂化原料的减压馏分油和减压渣油。
蒸馏塔内件——常压塔一般用板式塔盘。如各种浮阀塔盘、网孔塔盘;减压塔则常用压降小的各种填料,或填料与塔盘混用。
减压塔的操作可分为“干”式和“湿”式两种:
“干”式减压在减压炉炉管和减压塔底均不吹蒸汽,全塔压降和减压抽空负荷小,有助于提高减压塔拔出率,适用于燃料型减压塔。
对于生产润滑油原料的减压塔一般采用“湿”式操作。
转化工艺
转化工艺的作用就是将重质馏分或渣油转化成轻质产品。
炼厂的转化工艺分热转化和催化转化两类:
重质馏分油的热转化(热裂化)已基本不用,全部被催化转化(催化裂化、加氢裂化)所取代
渣油的转化则热转化(焦化、减粘裂化)与催化转化(渣油加氢)并存。处理金属含量和残碳高的渣油,目前还是以热转化为主
催化裂化
催化裂化是当前炼厂中最重要的转化工艺。自1942年第一套流化催化裂化开发以来,由于其独特优越性得到了飞快地发展。到2008年,全世界流化催化裂化加工能力已超过7亿吨/年。
与热裂化相比,催化裂化具有下列明显优点:
汽油产品的辛烷值高(RON88~92),氧化安定性好
反应速度快
气体产品中C1、C2烃类少,C3、C4产率高,可作为烷基化、醚化和化工产品的原料多,全球约有1/3的丙烯

高低并列式催化裂化反应再生系统
催化裂化主要操作参数有:
反应温度——反应温度是调节催化裂化转化率的主要变量,常用的反应温度为480~510℃。
反应压力——提高反应压力,增加了反应时间,从而可提高转化率,但压力过高,会导致焦炭产率增加,汽油和烯烃产率下降。对于反应压力要结合原料的生焦趋势和烟气能量回收的经济效益综合考虑,有烟气能量回收设施的反应压力一般为0.25~0.3MPa,无烟气能量回收的则为0.09~0.27MPa。
反应时间——反应时间过长,会增加二次裂化反应,使汽、柴油收率下降。在按汽油方案操作时,一般采用高反应温度和短反应时间(2~3秒);在按柴油方案操作时,则采用较低反应温度和较长反应时间,(3~4秒);渣油催化裂化一般控制在2秒左右。
剂油比——为单位时间内催化剂循环量与反应器总进料量的比值,它与反应时间对催化裂化反应在一定范围内有相似影响。剂油比受装置总热平衡所控制,一般当反应温度和再生温度不变时,剂油比也基本不变。
再生温度——无论是增加烧焦强度还是降低再生催化剂的含炭量,都必须提高再生温度。但再生温度也不能过高,除了受再生器的材料限制外,还会引起催化剂水热失活,一般再生温度不超过730℃,也不宜低于650℃。
再生催化剂炭含量——对沸石催化剂来说,催化焦炭主要沉积在沸石的活性中心上。因此再生催化剂炭含量对催化剂的活性影响很大,一般沸石催化剂的炭含量应保持在0.2%以下,最好在0.1%以下。
加氢裂化
加氢裂化实质上是催化加氢和催化裂化两种反应的综合,这种工艺可以用不同原料,有选择性的生产液化石油气、石脑油、柴油、喷气燃料等多种优质产品。
加氢裂化尾油又是生产优质润滑油和乙烯的原料,是炼厂中提高轻质油收率和提高产品质量的重要手段。
加氢裂化的主要反应有:
烷烃和烯烃的裂化,异构化和环化反应
烯烃的饱和反应
单环化合物的侧链断裂化或生成异构体
双环以上环烷烃发生异构裂环反应
稠环芳烃通过逐环加氢,裂化生成较小分子的芳烃及芳香环烷烃
加氢裂化催化剂是具有加(脱)氢功能和裂化功能的双功能催化剂。加(脱)氢功能由金属组分提供,常用的金属组分为Mo、W、Ni、Co,这些金属组分常组合使用。酸性功能由载体提供,常用的载体有无定型硅铝和沸石,二者可以单独使用,也可组合使用。
加氢裂化可以使用各种不同原料,但对原料中的杂质含量有要求。
原料中的有机氮化合物对沸石载体有明显的中毒作用。一般要求进加氢裂化反应器的进料氮含量<10ppm,为了保证达到这一要求,一般在加氢裂化反应器前设精制反应器,或者在裂化反应器中设精制段;
砷、铅等杂质也会使催化剂中毒,一般要求裂化反应器的进料中砷+铅含量不超过500ppm;
铁虽然对催化剂的活性影响不大,但铁盐沉积在催化剂上会使床层压降增大,所以要控制原料油铁含量<2ppm。
加氢裂化的工艺类型,根据反应特点可分为单段和两段二种工艺过程:
单段工艺过程中又分为在一个反应器中装一个或组合催化剂的工艺和使用二个反应器的单段串联馏程,其中第一个反应器为精制反应器,第二个为裂化反应器。
两段工艺过程则在一组反应器之间,反应产物要经气液分离和分馏,将气体及轻质产品进行分离,重质反应产物和未转化油再进入另一个裂化反应器。
如果按转化深度分,又可分为尾油循环和单程一次通过流程。
如果按反应压力分,可分为高压加氢裂化(反应压力在15MPa左右)和中压加氢裂化(反应压力在10MPa左右)。反应压力的选择主要决定于原料质量、转化深度及目的产品质量要求等。
根据目的产品不同又可分为中馏分油(喷气燃料、柴油)型和轻油型(重石脑油)。

一段加氢裂化工艺流程示意图
二段加氢裂化工艺流程示意图
加氢裂化的主要操作参数有:
反应压力——原料越重所需反应压力越高,提高反应压力,有利于转化率的提高,也有利于减缓催化剂表面积炭速度,延长催化剂寿命,但投资增加,常用的反应压力为10~20MPa。
反应温度——反应温度是加氢裂化工艺需要严格控制的操作参数。因为加氢裂化过程是强放热反应,反应温度增加,则反应速度加快,放出的热量也相应增加。如不及时从系统是将热量取出,势必引起床层温度骤升,导致催化剂超温升活,因此在各床层间要注入冷氢进行控制,常用的反应温度为370~440℃。
氢油比——提高氢油比,可以增加氢分压,有利于提高原料气化率,降低催化剂积炭速度,还可以有效地取出反应热,对重油加氢裂化氢油比一般为1000~1500(体积比)。
空速——调节空速可以控制加氢裂化反应深度,空速低,反应时间增加,反应深度提高,常用的空速范围为1.0~2.0h-1。
渣油加氢
早期的渣油加氢是为了生产低硫燃料油,自上世纪90年代以来,燃料油需求减少,需要将渣油进一步轻质化。为此渣油加氢主要用来为重油催化裂化提供原料,同时发生一定的裂化反应以获取部分柴油和石脑油。
渣油加氢按反应器的型式不同,可分为四类:
固定床渣油加氢 例如谢弗龙公司的RDS、VRDS工艺、UOP公司的RCD Unibon工艺。
沸腾床渣油加氢 例如鲁姆斯公司的LC-fining工艺、IFP的H-oil工艺
移动床渣油加氢 例如壳牌公司的Hycon工艺
浆态床工艺
延迟焦化
焦化是以贫氢的渣油为原料,在高温下进行深度热裂化和缩合反应的热转化过程,其目的是为了提高轻质油收率和生产优质石油焦。
在炼油厂中采用的焦化工艺目前有延迟焦化,流化焦化和灵活焦化三种,但占主要地位的是延迟焦化,到2008年,我国炼厂只有延迟焦化工艺,其产能已达4800万吨/年,最大的装置规模已达420万吨/年。
延迟焦化操作的关键是要控制原料油在加热炉管中基本上不发生结焦反应,而延缓至专设的焦炭塔中进行裂化、缩合反应。为了做到这一点,加热炉的设计是关键,加热炉的设计需要考虑:
要使原料油快速升温到500℃左右,必须提高炉管热强度,一般采用双面辐射炉。
为了尽量缩短油料在炉管内的停留时间,常采用较高的冷油流速(1.4~2.0m/s),并在适当位置向炉管内注水蒸汽。
加热炉管的在线清焦措施
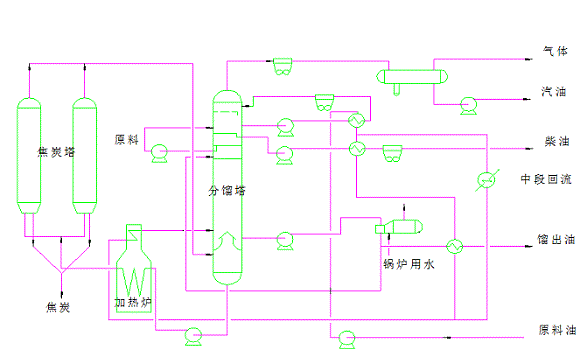
常规延迟焦化流程示意图
延迟焦化的化学反应,主要在焦炭塔内进行,随着油料的不断进入,塔内焦层逐渐升高。为了防止泡沫层冲出焦炭塔顶引起塔顶油气管线和分馏塔结焦,焦炭塔层上面应留有一定的空高,在有中子料位计监测时,空高可留3m左右,无料位计时则需5~6米。为了降低泡沫层高度,也可采取焦炭塔顶注入消泡剂的方法,但消泡剂大多为含硅化合物。硅对焦化馏出油后续加工装置的催化剂有不良影响。
焦炭塔为两个塔轮换操作当一个塔在进行反应充焦时,另一个塔在进行冷焦、除焦、预热等操作。切换周期,已从过去的24小时,缩短至16~18小时。焦炭塔的除焦,采用10~12MPa的高压水切割。冷焦水、除焦水现在可做到全部回用。
焦化轻质产品的质量比较差。焦化石脑油的辛烷值低,仅60左右,溴值高,安定性差;焦化柴油十六烷值较高,在50~60之间,氮含量高,因此都必须经过加氢精制。
焦化气体中,烯烃含量较少,经脱硫后可作制氢原料。
影响延迟焦化操作的主要工艺参数有:
反应温度——一般是指加热炉出口温度,反应温度太低,则焦化反应不足,易生成软焦、焦炭挥发分高,除焦困难。反应温度过高,焦化反应过深,会使汽柴油收率下降,焦炭变硬也会造成除焦困难,而且还使加热炉管易于结焦。因此反应温度常限制在495~505℃,在生产针状焦时,要采用变温操作,变化范围为460~510℃。
反应压力——一般指焦炭塔顶压力,反应压力对焦化的产品分布有一定影响,压力高,气体和焦炭产率增加,液收下降,焦炭的挥发分也会增加,因此在压力足以克服后部系统压力的前提下,尽量采用低的压力,通常为0.16~0.17MPa(表),但在生产针状焦时,反应压力要适当提高一些。
循环比——循环比对焦化产品的分布和装置处理量有影响,循环比大,焦化汽、柴油的收率增加,焦化馏出油收率减少。气体、焦炭产率上升,装置处理量减少,对一般焦化原料,循环比通常为0.05~0.5,为了提高焦化馏出油的产量以增加催化裂化或加氢裂化的原料,有采用小循环比的趋向。
减粘裂化
减粘裂化的目的是最大限度地降低渣油粘度,以节省燃料油调合时所需掺入的轻质油品,从而增加炼厂的轻质油收率。
减粘裂化是一种轻度热裂化的热转化工艺,早期的减粘裂化工艺流程与热裂化相似,反应物料在反应器内由上向下流动,反应温度高,停留时间长,开工周期短。上世纪70年代,开发成功上流式反应器,反应物料在反应器内由下向上移动,是一种低温(420~450℃),长停留时间的液相反应,反应器内设有筛板以减少返混。
减粘裂化汽、柴油的产率很低,而且质量较差,都必需经过加氢精制。
由于燃料油的需求减少,新建的减粘裂化装置很少,只有欧洲的炼厂,减粘裂化装置的加工量较大。
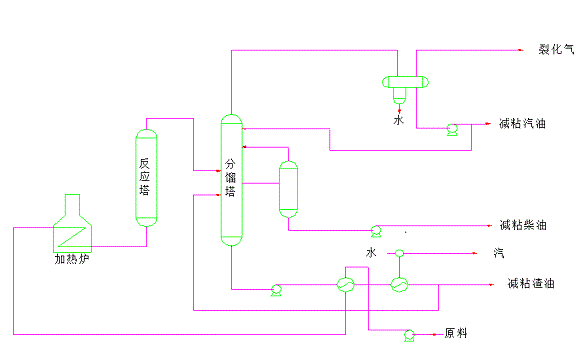
减粘裂化工艺流程示意图
精制和改质工艺
加氢精制(加氢处理)
加氢精制能有效地使原料中的硫、氮、氧等非烃化合物氢解,使烯烃、芳烃选择性加氢饱和,并能脱除金属和沥青等杂质,具有处理原料范围广、液体收率高、产品质量好等优点,是炼厂中最普遍使用的精制工艺。
由于含硫原油加工量愈来愈大,环境保护法规对油品质量要求和环境污染控制越来越严,加氢精制过程得到飞速发展,不仅汽、煤、柴等轻质油品需要进行加氢精制,对从含硫原油得到的催化裂化原料,也要经过加氢处理,以改善裂化产品的分布和减少SO2向大气排放。
加氢精制的主要反应如下:
加氢脱硫 如RSH+H2→RH+H2S
加氢脱氮 如R-CH2-NH2+H2→R-CH3+NH3
加氢脱氧 如 -OH → +H2O
烯烃加氢饱和 如R―CH=CH2+H2→R-CH2-CH3
芳烃加氢饱和 如 +4H2→
在上述反应中,脱硫反应比脱氮、脱氧反应比较容易进行,烯烃饱和容易进行,而芳烃饱和相对较难。
由于原料来源不同,杂质含量有很大判别,要达到相同精制深度,在操作条件和催化剂的选择上,会有显著不同。
l加氢精制的操作参数主要有:
è反应压力——提高反应压力,对轻质油加氢精制来说,有利于提高反应速度,但对重质油加氢精制来说,一方面有利于提高反应速度,另一方面又增加了混合组分中的液相比例,相应增加催化剂表面液膜对反应物的扩散阻力,从而降低了反应速度,因此最终影响须根据表面反应与扩散的相对速度而定。
提高反应压力,能有效地抑止催化剂表面积炭,有利于延长催化剂寿命,所以对压力的选择,既要考虑反应速度的需要,更要考虑催化剂的使用寿命。
对目前常用的Ni-W,Mo-Ni系催化剂,就脱硫而言,加氢精制压力(氢分压)一般为:
u直馏石脑油;
1.5~2.5MPa
u直馏柴油
2.5~3.5MPa
u二次加工汽油
2.5~3.5MPa
u二次加工柴油
3.5~6.5MPa
u减压馏分油
6.5~8.0MPa
反应温度——硫、氮化合物的氢解反应,反应速度随温度增加而增加,不受热力学平衡控制。而对硫、氮的杂环化合物以及芳烃的加氢饱和,为可逆反应,反应受平衡控制,因此有一极限温度,常用的加氢精制温度范围为250~420℃。
空速
——空速低,精制深度增加,但反应器容量和催化剂用量增加。在一定精制深度下,提高空速,必须相应提高反应温度,这会影响催化剂的使用寿命。合理空速的选择必须根据原料性质,精制深度要求,全面衡量。
对轻质油品的加氢脱硫、脱氮、烯烃饱和可用较高空速,石脑油可达2-8h-1,柴油可用1-3h-1,而对重质高含氮馏分油,即使提高压力、空速也只能在1.0h-1左右。
氢油比——提高氢油比可以增加氢分压提高反应速度,但超过一定值后,反应时间减少,反而会适得其反。提高氢油比有利于减缓催化剂结炭,延长催化剂寿命。但增加氢油比使能耗、氢耗增加,因此需要综合分析,才能选择合适氢油比,加氢精制一般采用的氢油体积比范围为:
石脑油 60~250
柴油馏分 150~500
减压馏分油 200~800

加氢精制工艺流程示意图
催化重整
催化重整是以C6~C11石脑油馏分为原料,在一定操作条件和催化剂的作用下,使烃分子发生重新排列,使环烷和烷烃转化成芳烃和异构烷烃并副产氢气的工艺过程,也可以说是一个石脑油改质的过程。
催化重整是炼油厂生产高辛烷值汽油,芳烃和氢气的主要工艺过程,在炼厂中占有十分重要的地位,对清洁汽油的生产,具有无法替代的作用。
进入重整反应器的原料,必须有合适的馏分并去除对催化剂有害的杂质。因此石脑油馏分必须进行预处理。
预处理一般包括预分馏和预加氢两部分,对含砷高的原料油,还包括预脱砷。
在预分馏部分,要切去原料中的轻、重组分,使进入重整反应器的原料按目的产品的不同符合下列馏程:
生产芳烃 65℃~160℃(170℃)
生产高辛值汽油 80℃~180℃
预加氢的作用是除去原料中的硫、氮、氧等杂质,经过预加氢后,进入重整反应器原料的杂质含量应小于下列指标:
氮 0.5 ppm
硫 0.5 ppm
砷 1 ppb
铅、铜 20 ppb
水 5 ppm
氯 1 ppm
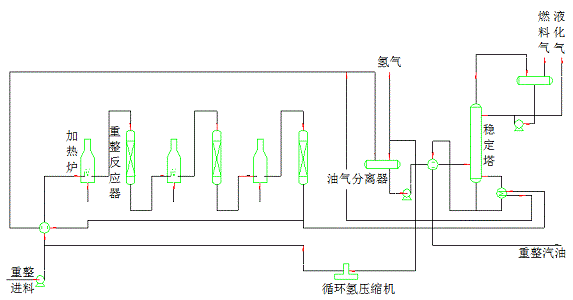
半再生式催化重整典型工艺流程示意图

UOP连续重整催化剂再生流程示意图
催化重整的主要操作参数有:
反应压力——反应压力低,液收,芳烃和氢产率都增加。自出现连续重整后,操作压力已降至3.5kg/cm2,但压力降低,会使催化剂失活加快。因此,半再生式重整的操作压力不能过低。
反应温度——重整反应总的热效应是吸热反应,因此高温有利于提高反应速率,但高温也会使催化剂积炭速率加快,因此对反应温度的选择要全面衡量,一般反应温度控制在480~520℃。
空速——空速的调节与催化剂性能和重整反应的动力特性有关,为了区别对待不同类型反应的特点,各个重整反应器的催化剂装入量不同,一般从一反到四反采用递增式装填。
氢油比——
氢油比大有利于降低催化剂失活速率,降低氢油比有利于环烷脱氢和烷烃脱氢环化反应的进行,并使能耗降低,因此一般是在可接受的催化剂失活速率下,将氢油比控制在较低范围内,常用的氢油比为5-8(摩尔比)
水氯平衡 ——氯可提供酸性功能,并有助于金属粒子的分散,如催化剂在操作过程中氯损失过多,会使活性下降,因此调整好水氯平衡,控制催化剂氯含量,十分重要。
对产芳烃的催化重整装置,应配有芳烃抽提和芳烃分馏设施。芳烃抽提过去多用甘醇类溶剂,新建设的则多用环丁砜作溶剂,因为环丁砜具有比重大,溶解性好,蒸发潜热小等优点,从而可降低能耗。
中压加氢改质(MHUG)工艺
催化裂化柴油中硫、氮、芳烃的含量高,十六烷值低,安定性差。特别是掺渣油的催化裂化,这些缺点更为突出,为此我国开发了以催化裂化柴油及其与直馏重柴油混合油为原料的中压加氢改质工艺。这种工艺使用加氢精制与加氢裂化组合催化剂,反应压力为6.5~10.0MPa。工艺流程与单段一次通过加氢裂化工艺基本一样。主要的产品有高十六烷值、低硫、低芳柴油,可作重整原料的重石脑油,可作乙烯裂解原料的加氢尾油,总的柴油产率可达55%,十六烷值>50。
吸附脱硫(S~Zorb)工艺
S-Zorb是美国康菲公司开发,主要用于催化汽油脱硫的工艺,该工艺采用吸附反应原理,可在辛烷值损失较小的情况下使催化汽油的含硫量降到小于10ppm。
燕山石化公司引进了我国第一套S-Zorb装置。已于2007年6月开工,规模为120万吨/年,处理硫含量为~300ppm的催化汽油,产品硫含量降至5~10ppm。
2007年中国石化公司整体收购这一工艺技术,对其专利有完全拥有权,可向全球进行技术转让。
S-Zorb工艺的操作条件约为:
反应温度 400~430℃
反应器总温升 20~35℃
反应压力 ~30MPa
反应空速 Whsvh-1 3-5
氢油比(mol比) ~0.3
再生温度 500~510℃
再生压力 0.1~0.15MPa
炼厂气体加工工艺
烷基化工艺
异丁烷和烯烃(C3=、C4= 、C5=
)在酸催化剂作用下生成的烷基化油。辛烷值高(RON93-95,MON92-93)辛烷值的敏感性小,具有理想的挥发性和清洁的燃烧性,是汽油的理想调合组分。
在国外炼油厂中烷基化是应用最广、最受重视的气体加工工艺。几乎所有国外大型炼厂中都有烷基化装置。
烷基化工艺采用酸强度高,酸中心多的硫酸或氢氟酸作催化剂。
硫酸法烷基化与氢氟酸法烷基化在装置投资,操作费用,产品质量和产品收率等方面都十分接近,因此两种方法能长期共存,都被广泛采用。但这两种方法都有其独特的缺点,硫酸法烷基化存在稀硫酸难以处理,而氢氟酸则有剧毒的危险。
酸耗在烷基化的操作成本中占的很大比重。原料中的水和二烯烃都会使酸耗增加。因此原须经过脱水和选择加氢
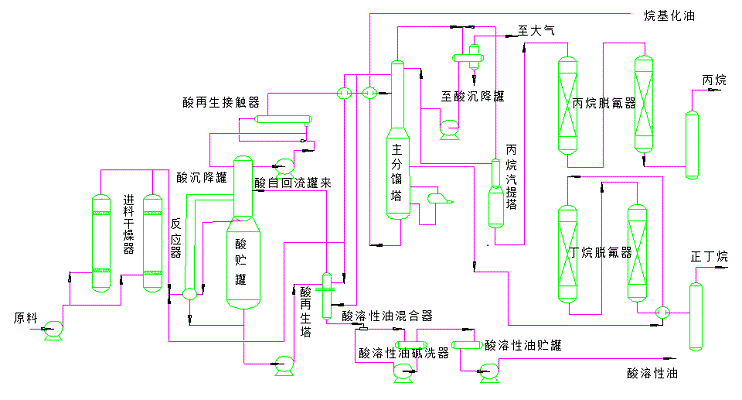
飞利浦斯氢氟酸烷基化工艺流程示意图
烷基化的主要工艺参数有:
反应温度——烷其化反应是放热反应低温有利于反应的进行,但温度过低则会使异丁烷在酸中的溶解度降低,酸的粘度上升,从而影响烷基化油质量。
反应温度对硫酸法的影响比对氢氟酸法更大,通常硫酸法烷基化的反应温度为4~10℃,氢氟酸法为21~40℃,因此硫酸法烷基化需要致冷措施,现在采用的致冷有两种方式即氨闭路循环致冷和反应流出物自蒸发致冷。
反应压力——压力在烷基化反应过程中的唯一作用就是保证反应物料处于液相,一般为0.3~0.8MPa。
酸浓度——在反应过程中,酸会被反应过程中生成的水稀释和被烃类副产物污染使酸的活性下降。硫酸法烷基化所用的新酸浓度一般为98%,排出废酸的浓度为88~90%。当酸浓度为95~96%时,烷基化油的辛烷最高。氢氟酸烷基化酸浓度一般控制在85~90%;浓度过高,对反应反而不利。
MTBE(甲基叔丁基醚)生产工艺
异丁烯和甲醇在强酸性阳离子交换树脂作用下生成的MTBE,是良好的高辛烷汽油调合组分,其MON为101,RON为117,而且有良好的调合效应,其调合辛烷值均高于其净辛烷值。MTBE还可提高汽油的安定性及减少汽车尾气排放污染物。
尽管美国由于发现MTBE污染了地下水而禁止在汽油中添加,世界上其它国家都没有禁止。
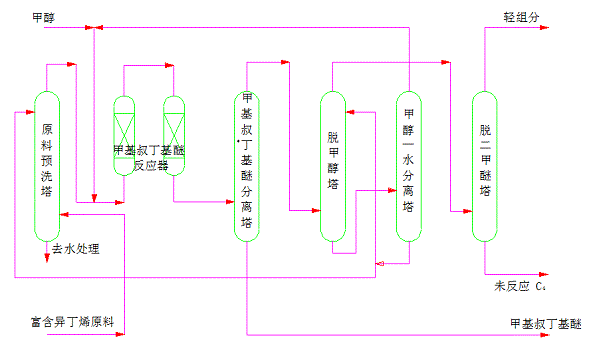
常规法合成MTBE流程示意图
MTBE工艺的反应操作条件如下:
醚化反应器入口温度 40℃
醚化反应器出口温度 58~60℃
反应器压力
一般为1~1.5MPa
混相床为0.7MPa
醇烯比(mol比) 1~1.2
空速 1~2 h-1
催化裂化干气中乙烯与苯烃化制乙苯工艺
催化裂化干气中含有一定量的乙烯,其利用有二种途径:一是用变压吸附法将乙烯提浓后送到乙烯裂解的分离部分,变成聚合级乙烯再加以利用;另一是将干气中的稀乙烯直接与苯烃化生产乙苯。我国利用自行开发的技术,已建成了多套工艺装置。

润滑油生产工艺
润滑油是重要的石油产品,其用量远较运输燃料为少,而且制造工艺比较复杂,因此在国内外润滑油集中在少数炼厂生产。
不是所有原油都可以生产好润滑油的,长期以来,人们都把石蜡基原油作为生产润滑油的首选原油,因为石蜡基原油中烷烃和长侧链环烷烃含量较多,芳烃和非烃类(杂原子有机化合物,胶质、沥青质)物质含量较少,可制得粘-温性能较好的润滑油基础油,其次是环烷基原油,可利用其凝固点低的特点,制取某些要求倾点很低而不要求粘温性能的专用润滑油如寒区变压器油,冷冻机油,金属加工用油等。
润滑油生产的工艺结构基本可分为三类
物理加工工艺
全氢法生产工艺
用全氢法生产的润滑油质量最好,但投资和操作费用较高
混合加工工艺
溶剂精制工艺
溶剂精制是一个物理萃取分离过程。利用溶剂的溶解性和选择性,将油料中的非理想组分溶于大量溶剂中,然后与理想组分和少量溶剂进行二相分离,再分别进行溶剂回收后得精制油和抽出油。
溶剂脱蜡工艺
油料中的蜡在低温时会从油中结晶析出,因而可用过滤方法将其分离。但低温下油的粘度增加,也不利于蜡晶粒的长大,使蜡与油的分离困难,因此加入溶剂加以稀释,所以称为溶剂脱蜡。
脱蜡溶剂一般用极性溶剂和非极性溶剂的混合溶剂,极性溶剂(如各种酮类)有较好的选择性,但溶解能力差;非极性溶剂(如苯、甲苯),则有较好的溶解能力。
我国炼厂中过去用丙酮-苯-甲苯三元溶剂,现在则多使用甲乙基酮-甲苯二元溶剂,酮与甲苯的比例,则因原料而异,一般处理轻质油料时甲乙酮比例较大。
溶剂脱沥青工艺
减压渣油中除含有可生产重质润滑油的组分外,还含有沥青质、胶质、硫、氮、氧等非烃化合物,溶剂脱沥青工艺就是要用溶剂脱除这些非理想组分的过程。
以丙烷作溶剂,脱沥青的选择性最高,脱沥青油的品质最好,因此国内外生产润滑油的脱沥青工艺,都以丙烷作溶剂,如脱沥青的目的产品为催化裂化原料,则要选用丁烷,戊烷等溶解性能好的作溶剂。
很多溶剂脱沥青工艺采用一次抽提二段沉降流程,可同时得到轻、重脱沥青油,分别用作润滑油原料和催化裂化原料。
润滑油加氢处理是使润滑油原料中的多环芳烃开环,使之成为粘度指数高的少环多侧链芳烃或环烷烃,而不是像溶剂精制那样将这些非理想组分抽提掉。
加氢处理用的催化剂为双功能催化剂,但裂化功能不能太强,因此载体的酸性不能太强,酸性中心也不能太多。
加氢处理由于要使多环芳烃加氢并裂化,所以加氢温度和压力都很高。
总压一般大于15MPa
温度为360~420℃
液时空速为0.3~1.0h-1
氢油比一为1000~1800
润滑油加氢脱蜡
润滑油加氢脱蜡是上世纪70年代后期发展的新工艺,由于这种工艺生产的润滑油质量好,收率高,因此逐渐受到重视。加氢脱蜡由于所用催化剂不同,可分为两种类型:一种是将烷烃异构化,称为异构降凝,例如谢弗龙公司的Isodewaxing工艺
另一种是将烷烃选择性裂解,如摩比尔公司的MLDW工艺。
异构降凝采用含有贵金属(如
)的催化剂,因此对原料中要求的杂质含量很严,要求氮<2ppm,硫<10ppm,其操作条件为
反应压力 7~20MPa
反应温度 300~430℃
空速 0.5~1.5h-1
我国已引进了这种技术。
选择性裂化型加氢脱蜡利用以丝光沸石或Zsm-5沸石为载体的催化剂,利用载体的均匀孔结构和特殊的吸附性能,让凝点较高的正构烷烃和带短侧链的异构烷烃发生裂化反应,其操作条件大致为
反应压力 1.5~5.5MPa
反应温度 280~360℃
空速 0.5~3h-1
润滑油补充精制
经溶剂精制和溶剂脱蜡后的润滑油组分,常含有少量溶剂及少量杂质,影响润滑油的颜色和安定性,因此需要进行补充精制、最早采用白土补充精制。由于存在收率低,白土废渣污染环境等缺点,已逐渐被加氢精制所取代。
加氢补充精制使用Ni-Mo,W-Mo型催化剂,操作条件非常缓和:
反应压力 2~6MPa
反应温度 210~320℃
空速 1~3h-1
氢油比 50~300
这一工艺过程基本不改变润滑油料的烃类结构和组成。
Copyright © 2015www.CV3000.com